Our Packaging Supply
Improvement Process
A Process That Ensures Partnership
Our Packaging Supply Improvement Process (PSIP) Team partners with customers to drive continuous improvement and eliminate inefficiencies in their supply chains. It's a collaboration that benefits each customer's ability to grow their business and ensure a long-term partnership.
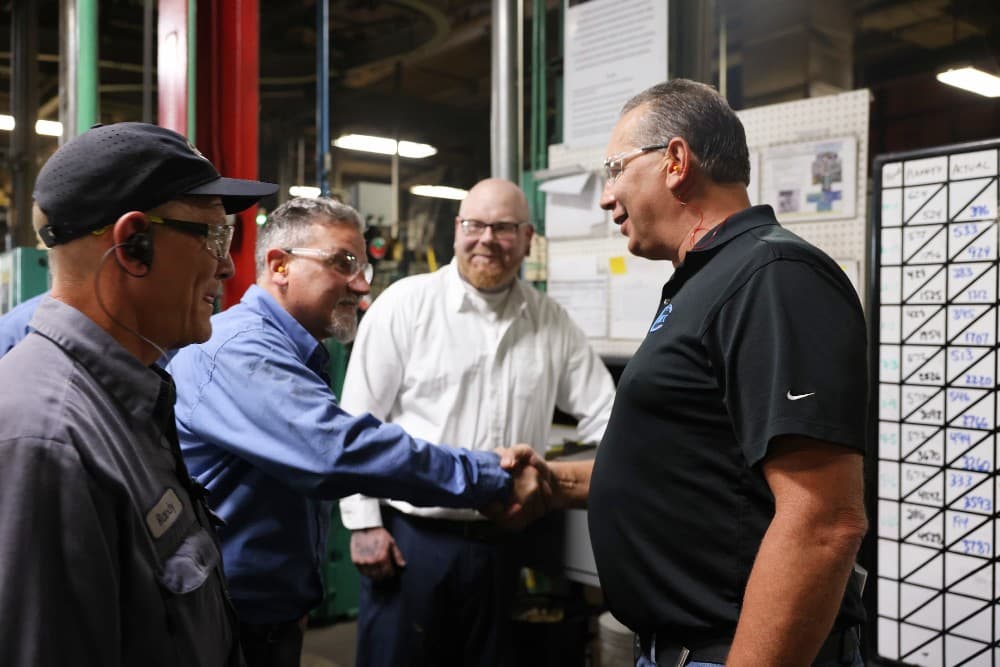
What Drives Our Commitment to Continuous Improvement
Our PSIP team will diagnose improvement opportunities through a value stream analysis.
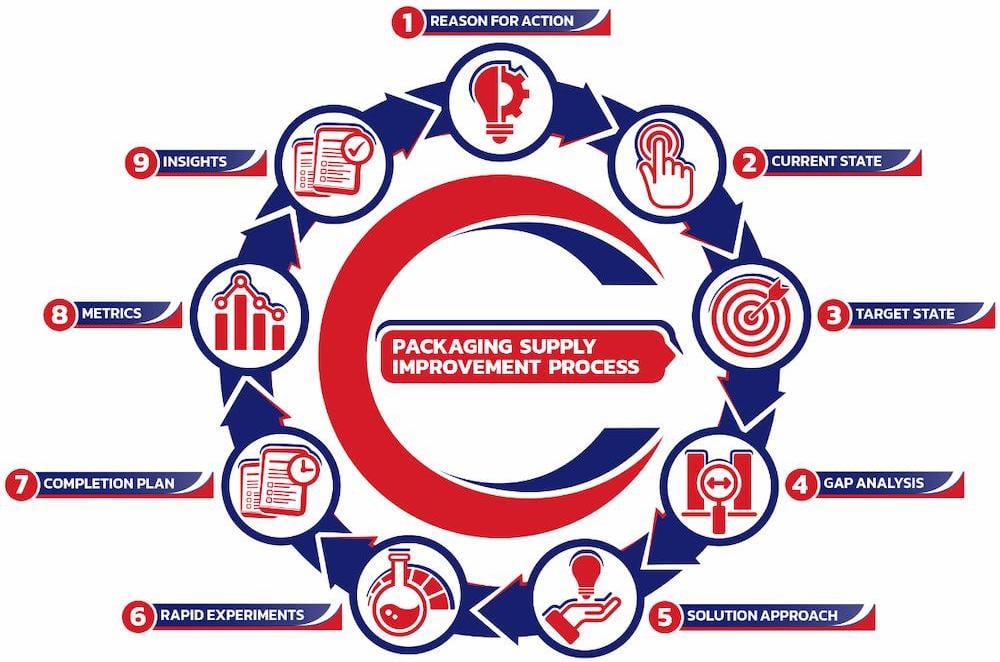
Learn what we can accomplish within 90 days using our Packaging Supply Improvement Process. Contact us for more information.
What Our PSIP Process Helps Improve
Our PSIP team will be your partner in identifying areas that have room for improvement.
Vendor Management
Label Installation
Visibility of Order & Delivery Information
SKU Optimization
Delivery Methods
Technical Resources
Palletizing
Ordering Methods
Supply Chain Complexity
Continuous Improvement
Process Improvement Techniques
Overcoming a Labor Shortage
Challenge: A customer was struggling to find labor to meet their filling requirements. This was causing both extended lead times and significant overtime.
Our PSIP Solution: The North Coast Container team provided palletizing and labeling solutions to reduce extended lead times and significant overtime.
Reducing SKUs
Challenge: A customer was unable to reduce SKUs after the company completed multiple acquisitions and divestitures.
Our PSIP Solution: The North Coast Container team worked with the customer to identify a solution to optimize SKUs.
Providing Innovation & Partnership
Challenge: A customer was constantly running out of material, which was causing facility downtime and frustration.
Our PSIP Solution: The North Coast Container team identified solutions to eliminate downtime and frustration, which resulted in weekly restocking and eliminated customer headaches.